
This means that the state of stress and deformation below a horizontal centerline is a mirror image of that above the centerline, and likewise for a vertical centerline. The uniform, homogeneous plate above is symmetric about horizontal axes in both geometry and loading.
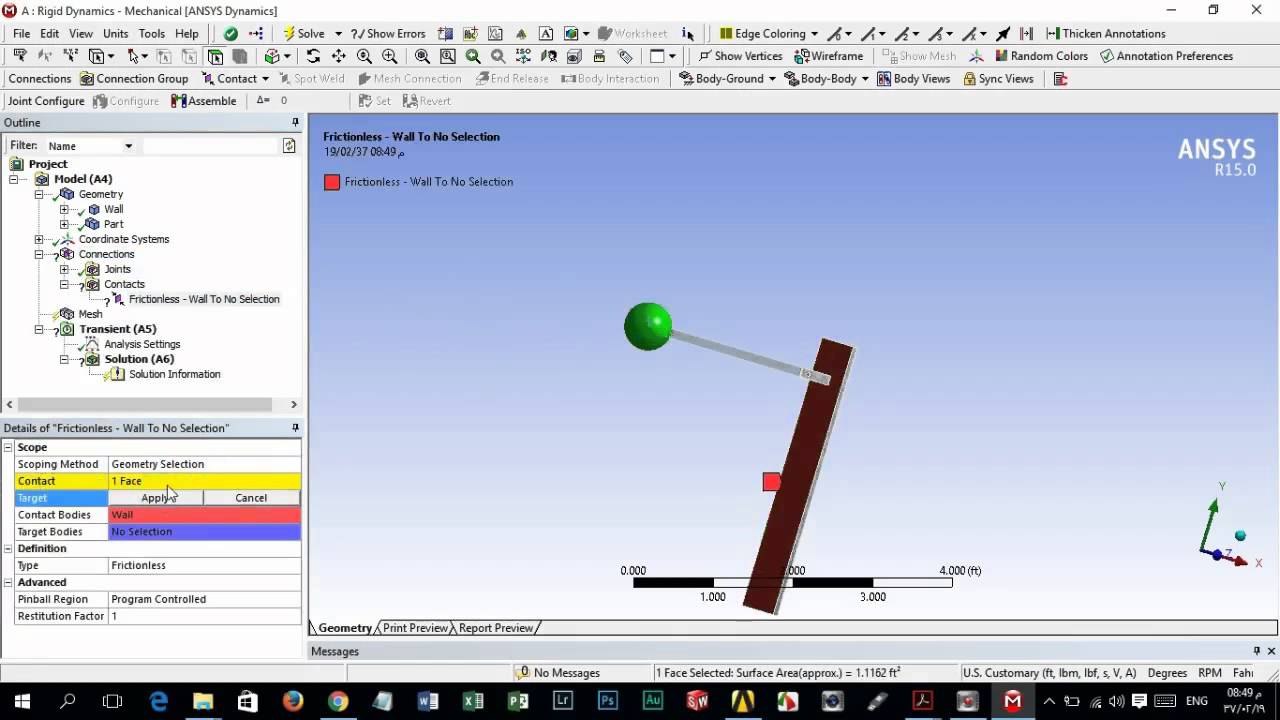
The results of these studies are widely published, and we can look up the stress concentration factor (e.g., from the ME533 textbook) for the case shown above. We apply a horizontal tensile loading in the form of a pressure p = 1.0 N/ m2 along the vertical edges of the plate.īecause holes are necessary for fasteners such as bolts, rivets, etc, the need to know stresses and deformations near them occurs very often and has received a great deal of study. It is made of steel with material properties elastic modulus, E = 2.07E11 N/m2 and Poisson's ratio, = 0.29. The 1.0 m x 0.4 m plate has a thickness of 0.01 m, and a central hole 0.2 m in diameter. The problem is that of a tensile-loaded thin plate with a central hole as shown in the figure below. To start off, let's solve a problem with a known solution so that we can check our understanding of the FEM process. We will use both triangles and quads in solution of the example problems that follow. A thin beam loaded in it plane and a spur gear tooth are good examples of plane stress problems.ĪNSYS provides a 6-node planar triangular element along with 4- and 8-node quadrilateral elements for use in the development of plane stress models. Further, the stresses, , and are all zero for this kind of geometry and loading. The non- zero stresses, , and lie in the X-Y plane and do not vary in the Z direction.
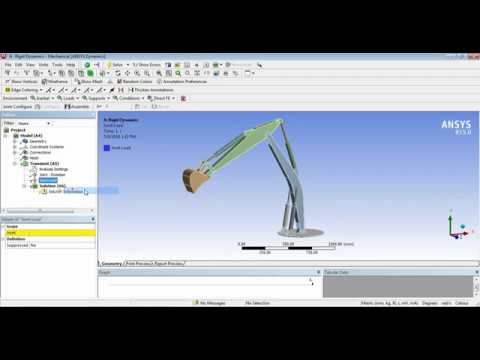
Let the X-Y plane be the plane of analysis. However, two-dimensional models are often easier to develop, easier to solve and can be employed in many situations if they can accurately represent the behavior of the object under loading.Ī state of Plane Stress exists in a thin object loaded in the plane of its largest dimensions. In general, the analysis of such objects requires three-dimensional modeling.
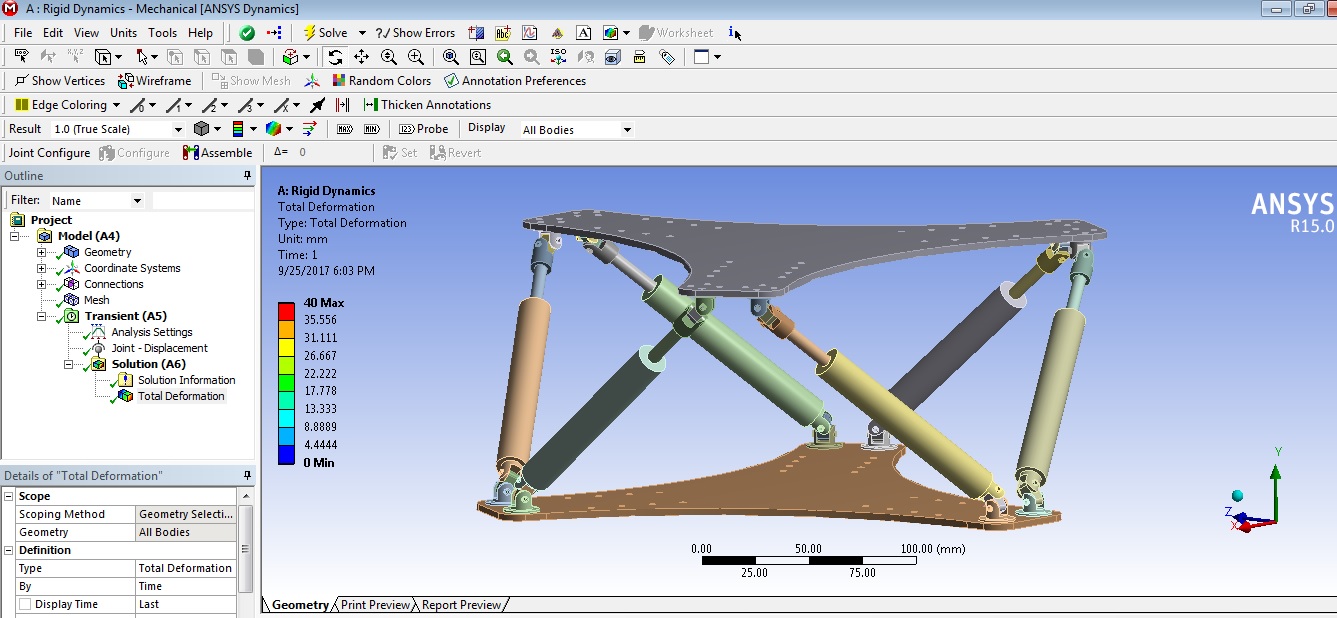
When referenced to a Cartesian coordinate system these components of stress are: It is possible for an object with arbitrary shape to have six components of stress when subjected to three-dimensional loadings. Using the various ANSYS 2D element formulations.Evaluating potential errors in the solutions.Solving planar stress concentration problems.The tutorials in this lesson demonstrate: Plane s1ress and plane strain problems are an important subclass of general three- dimensional problems. HOLE TUTORIAL 2 (1) PREPROCESSING 4 (2) SOLUTION 6 (3) POSTPROCESSING 6 (4) MORE POSTPROCESSING 9 (5) ANSYS GEOMETRY 12 (6) THE APPROXIMATE NATURE OF FEM 14 (7) USING THE FULL MODEL 15 4.
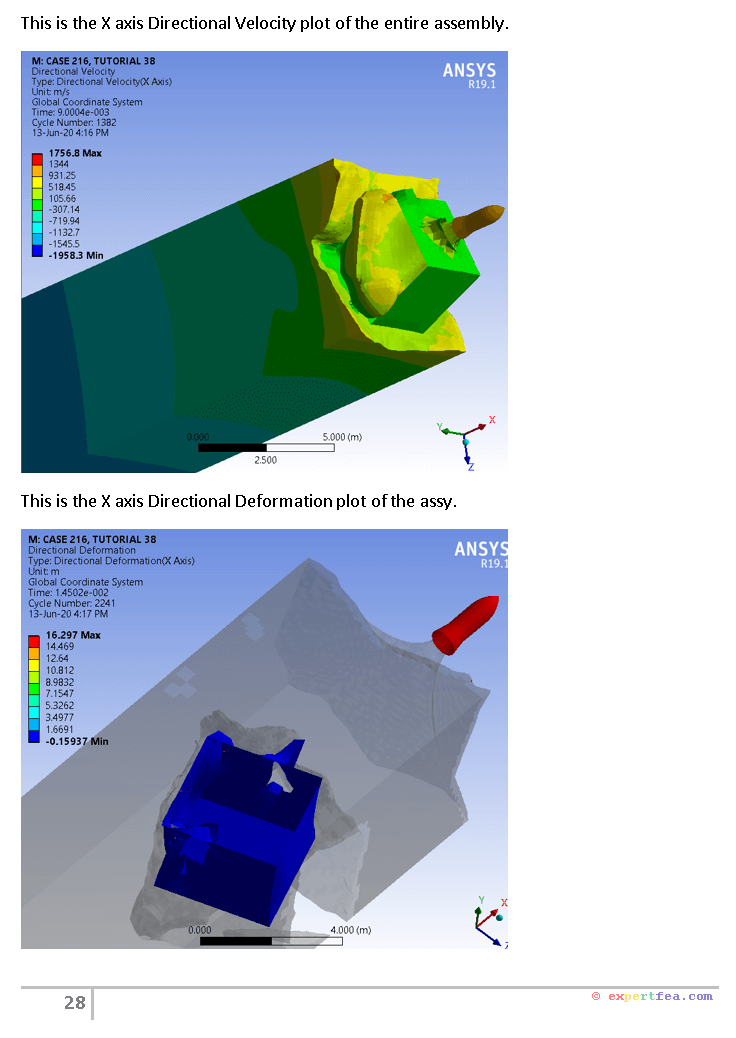
Xin Mechanical and Nuclear Engineering Kansas State Universityġ.
